Safety Management Organizational Culture
I would like to provide an on-site report regarding the high level of safety management expanded to a whole organization to achieve zero accidents in Japan.
In the railway industry an accident can cause damage to both passengers and railway personnel. Moreover, delay and suspension of operation may have a direct and tremendous impact on people’s lives in society. Therefore, zero accidents are a must-achieve target.
There is a major private railway company operating railway lines in Tokyo and Kanagawa. From top management to new employees, they work together to achieve zero accidents with the slogan “Safety-sensitive culture for the whole organization”. The head office and their railroad workers are working in close cooperation to build an organization that can achieve the following tasks: visualization of field information, analysis of the real facts and background of an accident, and using imagination and insight to prevent an accident.
For example, they fix the 19th of every month as safety day and all division chiefs make their rounds of the working sites. In addition, the managing staff, including top management, brainstorms about things such as the best way to improve the general atmosphere on the working site, or how to have better communication in the organization as a whole. Alert messages are sent to the CEO’s mobile phone when a train is expected to be delayed more than 15 minutes. I also learned that employees working at the station were encouraged to make suggestions for safety improvement in order to prevent accidents. For example, “The stairs on our station are slippery and dangerous”, or “Sunlight can sometimes make the signals difficult to be recognized.” As every kind of accident imaginable could never happen, our industry can learn a lot from this company on implementing measures that make the workplace safe.
On the way home after this interview, I swore to myself that I wouldn’t rush into a train even if I’m in a hurry.
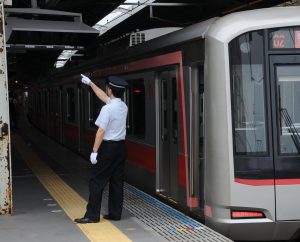
Safety management for the whole organization